Yodify Product Library
Instantly add the The Xs S System and 50,000+ more product series to your store or catalog
Book Your Demo and See How
or create your store
The Xs S System
Brand: GeoRocFor Accessories IncThe life of this system is extended due to its geometry. The crown has an internal shoulder (doughnut) to receive impact directly from the driver providing the necessary force to drill and drive down casing.
Having a “socket type” assembly fitting over the casing which allows for better welding alignment.
No other system on the market will tolerate the use of a hammer as big as the Xs S drilling system
When working with heavy wall casing, we recommend the use of the Xs T drill, which is made especially to give maximum clearance for sub-casing drilling.
Components:
Driver Bit
The driver bit is the device that transfers impact and rotation to the crown bit for drilling. The driver bit locks into two flats on the casing crown and they act together as a standard drill bit, both the driver bit and the crown have tungsten carbide buttons. The Driver bit drills a pilot hole below the crown to guide the direction of the casing in rough drilling. Afterwards this pilot space below the crown allows the square bit to turn without touching the crown.
The driver bit is the device that transfers impact and rotation to the crown bit for drilling. The driver bit locks into two flats on the casing crown and they act together as a standard drill bit, both the driver bit and the crown have tungsten carbide buttons. The Driver bit drills a pilot hole below the crown to guide the direction of the casing in rough drilling. Afterwards this pilot space below the crown allows the square bit to turn without touching the crown.
Crown Bit
The crown bit is a two-piece unit permanently connected together. The upper part is welded to the casing, and the lower part, which has Tungsten Carbide is free to rotate with the driver bit.
The crown bit is a two-piece unit permanently connected together. The upper part is welded to the casing, and the lower part, which has Tungsten Carbide is free to rotate with the driver bit.
Square Bit
The drill through bit is specially shaped to pass through the crown’s flats, and to drill the sub-casing hole to a maximum hole diameter, enabling in most of the cases, the use of a larger diameter hammer than the competition.
- Impact zone: Direct energy from the hammer is transferred to the crown bit through two (2) recesses formed by the locking surface plus another contact zone all around the periphery of the driver (donut).
- Evacuation: Two (2) big air holes are drilled in the face of the bit (drilling end). Those holes are directly connected to two (2) large flushing air ways, this transfer the drill debris from the drilling end of the driver up in the casing. To help the evacuation of debris, two (2) smaller air holes in the flushing air ways, gives the cuttings some velocity.
This model also comes with a “rotational-crusher zone”. That protective zone is placed at the end of the flushing air ways, just under the hammer spline drive. This zone (patent pending) is to improve the evacuation by preventing accumulation of rocks and gravel at a recess point. By turning the driver against a fix casing, the rock is crushed in smaller particles and then evacuated through the casing.
Features- Straighter Holes: Because this ring bit system doesn’t use any eccentric parts, it will drill in any type of overburden with practically no deviation. The driver bit design has a pilot portion that drills 3″ to 5″, ahead of the crown bit, allowing it to keep the casing very straight. If you try to drill on the side of a boulder with an eccentric system, the reamer will kick you out of your trajectory.
- Better Rate of Penetration: there are two (2) distinct advantages when drilling with the Xs drill system:
- 1 – Concentric: On the crown bit, there are carbide buttons all around the periphery of the hole, as opposed to approximately one third (1/3) on an eccentric system. That means that for each turn you do with our ring bit, you have in fact drilled a deeper portion of the hole compared to drilling with any eccentric design.
- 2 – Hammer: If you have a lot of boulders, or if you need to drill in fractured rock, the Xs is the only system offering the advantage of using a larger hammer to drill with the crown. The penetration rate through boulders will be comparable to drilling with a conventional oversized bit.
- Smooth Drilling: Compared to an eccentric method, drilling with the full face Xs drill system will be an unbelievable experience. Working with an eccentric system is very hard on every piece of equipment due to excessive torque applied by the reamer on the driver device, hammer, drill rods, rotation head and mast.
- Wear on gage carbide button: The wear on the carbide buttons on an eccentric system (on the pilot and especially on the reamer part) will occur very fast, especially in abrasive rock or harder ground conditions. On the Xs drill system, there is double the quantity of carbides on the gage row that are actually needed to give extended life.
- Components: Eccentric systems consist of a lot of different components, all necessary for its operation. Usually there is a pilot bit, a reamer bit, a driver, steel balls, set screws, pins, spring pins, etc… if you are using a wing type system, a driver device, 2, 3, or 4 wings, pins, screws, spring pins, etc.. All these parts are very costly and this can cause you lot of time on a job site. With the Xs drill system, there is a driver and an assembled crown ready to drill. That’s it !
- Toughness of parts: In eccentric and/or wing bit systems, all components are very fragile, and as soon as you have a little bit of wear in overall system, those parts are inclined to break without notice and leave you again with down time.
- Direct Energy Transfer: With the Xs drill system, the energy given by the hammer is transfer directly and entirely to the drilling part of the crown bit, and not to a driving shoe.
- Easier to Weld: The crown bit is composed of two (2) assembled swivel parts. The lower rotating part which has carbide buttons to drill, receives the impact and rotation from the hammer. The upper part is welded to the casing, but doesn’t receive any percussion directly from the hammer but is pulled down with the casing through a swivel joint. The impact to the joint is minimized because the drilling action of the rotating crown portion has absorbed most of it, leaving however enough energy to pull down the casing.
- Less Maintenance: In almost any other system, there is a lot of maintenance to do on the most expensive part which is the driver device. The driving shoe is fixed to the casing and the driver rotates and impacts on the upper shoe causing rapid wear to appear on the driver which then needs to be rebuilt or replaced. On the Xs drill system, that grinding effect is transferred to the swivel joint between the upper and lower part of the crown, which in 90% of cases is left in the hole.
1 - 12 of 18 Part Numbers
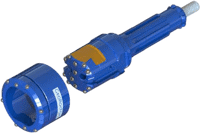
XS-S-CR10.75/PLUS
- Casing OD - 10.750"/273 mm System Measurement
- Crown Type - Standard Crown
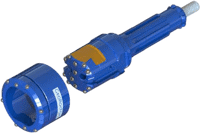
XS-S-CR10.75/SA
- Casing OD - 10.750"/273 mm System Measurement
- Crown Type - SA Crown (severe application)
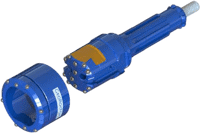
XS-S-CR4.50/PLUS
- Casing OD - 4.500" / 114.3 mm
- Crown Type - Standard Crown
- Maximum Wall - 0.197"/5 mm
- Hammer Size - 3"/3,5"
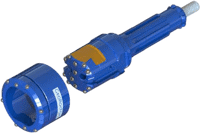
XS-S-CR4.50/SA
- Casing OD - 4.500" / 114.3 mm
- Crown Type - SA Crown (severe application)
- Maximum Wall - 0.197"/5 mm
- Hammer Size - 3"/3,5"
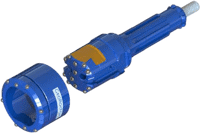
XS-S-CR5.00/PLUS
- Casing OD - 5.000" / 127 mm
- Crown Type - Standard Crown
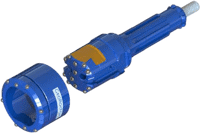
XS-S-CR5.00/SA
- Casing OD - 5.000" / 127 mm
- Crown Type - SA Crown (severe application)
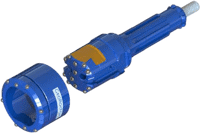
XS-S-CR5.50-B/PLUS
- Casing OD - 5.500" / 139.7 mm -B System Measurement
- Crown Type - Standard Crown
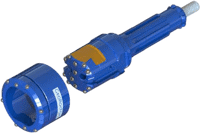
XS-S-CR5.50-B/SA
- Casing OD - 5.500" / 139.7 mm -B System Measurement
- Crown Type - SA Crown (severe application)
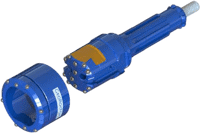
XS-S-CR5.50/PLUS
- Casing OD - 5.500" / 139.7 mm
- Crown Type - Standard Crown
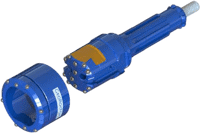
XS-S-CR5.50/SA
- Casing OD - 5.500" / 139.7 mm
- Crown Type - SA Crown (severe application)
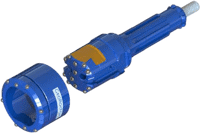
XS-S-CR6.00-B/PLUS
- Casing OD - 6.000" / 152.4 mm -B System Measurement
- Crown Type - Standard Crown
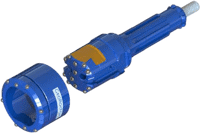
XS-S-CR6.00-B/SA
- Casing OD - 6.000" / 152.4 mm -B System Measurement
- Crown Type - SA Crown (severe application)
1 - 12 of 18 Part Numbers
Specifications
Casing OD
- 4.500”/114.3 mm
- 5.000”/127 mm
- 5.500”/139.7 mm
- 6.000”/152.4 mm
- 6.625”/168.3 mm
- 7.000”/177.8 mm
- 8.625”/219 mm
- 10.750”/273 mm
Maximum Wall
- 0.197”/5 mm
- 0.312”/7.9 mm
- 0.188”/4.8 mm
- 0.375”/9.5 mm
- 0.393”/10 mm
- 0.250”/6.4 mm
Crown Outer Diameter
- 5.250”/133.4 mm
- 5.750”/146 mm
- 6.250”/158.8 mm
- 6.000”/152.4 mm
- 6.500”/165.1 mm
- 7.500”/190.5 mm
- 8.000”/203.2 mm
- 9.500”/241.3 mm
- 11.750”/298.5 mm
Crown Inner Diameter
- 3.900”/99.1 mm
- 4.180”/106.2 mm
- 4.875”/123.9 mm
- 4.530”/115 mm
- 5.050”/128.3 mm
- 6.060”/153.9 mm
- 6.400”/162.6 mm
- 8.060”/204.7 mm
- 9.700”/246.4 mm
Crown A/F
- 3.450”/87.6 mm
- 3.780”/96 mm
- 4.375”/111.1 mm
- 4.060”/103.1 mm
- 4.570”/116.1 mm
- 5.660”/143.7 mm
- 5.900”/149.6 mm
- 7.530”/191.3 mm
- 8.960”/227.6 mm
Driver OD
- 4.050”/102.9 mm
- 4.330”/110 mm
- 5.060”/128.5 mm
- 4.700”/119.4 mm
- 5.170”/131.3 mm
- 6.220”/158 mm
- 6.560”/166.6 mm
- 8.200”/208.3 mm
- 9.940”/252.5 mm
Sq. Bit OD
- 3.850”/97.8 mm
- 4.125”/104.8 mm
- 4.813”/122.3 mm
- 4.500”/114.3 mm
- 5.000”/127 mm
- 6.000”/152.4 mm
- 6.375”/161.9 mm
- 8.000”/203.2 mm
- 9.625”/244.5 mm
Hammer Size
- 3”/3,5”
- 4”
- 5”
- 5”/6”
- 6”
- 8”
- Water Well
- Geothermal Well