Yodify Product Library
Add the LRT 622 Recycling plant to your store or catalog
Book Your Demo and See How
or create your store
LRT 622 Recycling plant
Brand: LiebherrThe LRT 622 in trough shape is the perfect recycling plant for high washing capacities of up to 20 m³/h and is characterised by custom configurations.
Future needs recycling! Liebherr concrete recycling systems ensure that residual concrete and cleaning water are recycled in an environmentally friendly manner.
Residual concrete is treated in a way so that all the constituents can be re-used. The environment therefore incurs no additional burden at all.
Reduction of environmental impact Every day, the production of concrete means that quite large amounts of residual concrete and also cleaning water from batching plant and truck mixers must be processed.
These residues must not be allowed to impose a burden on the environment. Our innovative washing-out units enable environmentally conscious use of materials on the site.
Liebherr recycling plants are suitable for returned concrete from the site, as well as for washing water and residual concrete from cleaning batching plants, truck mixers and concrete pumps.
Material savings Sand and gravel are washed out cleanly and re-used as production aggregates. Water savings Since everything can be re-used, both material and process water are saved when new concrete is produced.
The residual water from recycling can easily be returned to the production process. The gantry used to wash out truck mixers can also be supplied with water recovered in this way.
The remaining water containing cement is collected in a vat and maintained in suspension by an agitator.
A proportion of this water can be returned to the concrete mixer without any reduction in the quality of the finished product.
Features- Flexible concept The concrete recycling plant type LRS is supplied in five various versions and sizes.
- Little space requirement All these units are compact in layout and therefore occupy very little space where they are set up.
- Low maintenance and effective wear protection The screw is located at a predetermined spacing in the housing, so that a bed of material is built up and unnecessary wear is effectively avoided.
- Time and money saving The loading hopper is specially shaped so that it can be filled from various angles from one or two truck mixers. It is also designed to prevent accidental overfilling. The discharge height permits a generous storage volume. The plant has a screen cut down to 0.25 mm or below.
1 - 6 of 6 Part Numbers
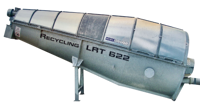
LRS 606/LRS 606 mobile
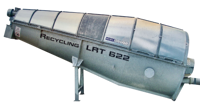
LRS 708
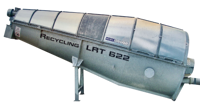
LRS 806
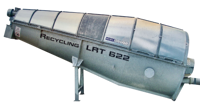
LRS 908
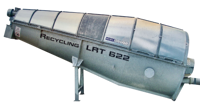
LRT 422
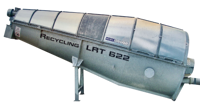
LRT 622
1 - 6 of 6 Part Numbers
Specifications
Brand
Trough length
- 6,000 mm
Trough diameter
- 2,200 mm
Power of mixer main motor
- 11.0 kW
Height of solid material discharge
- 2,000 mm
Discharge hopper width
- 2,000 mm
Large discharge hopper width
- 3,000 mm
Truck mixer-discharge points
- 1 - 2
Output ca.
- 20 m³/h
Size of the residual water basin
- Project related depending on the number of truck mixers and concrete pumps
Separating cut
- 0.25 mm
Max. standard grain size
- 35 mm